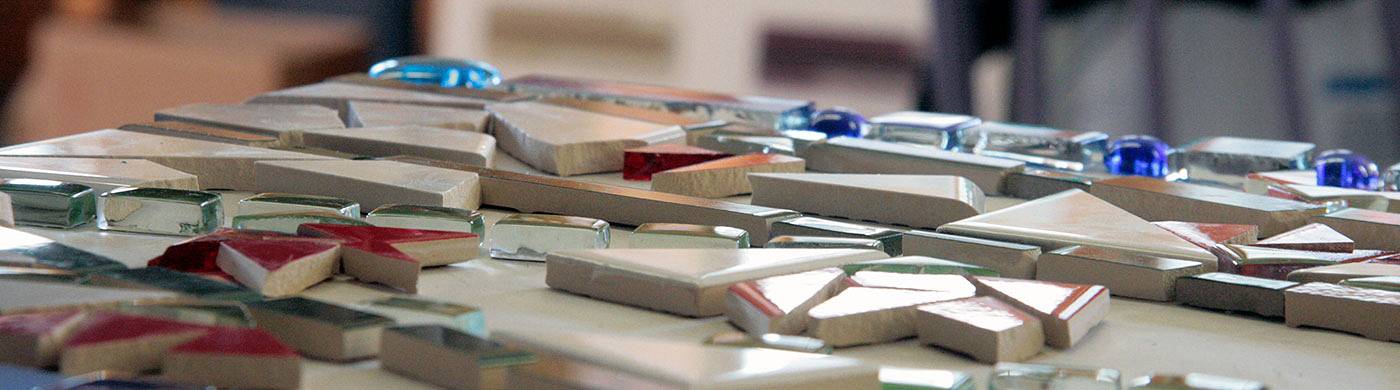
The Tog and the Thel
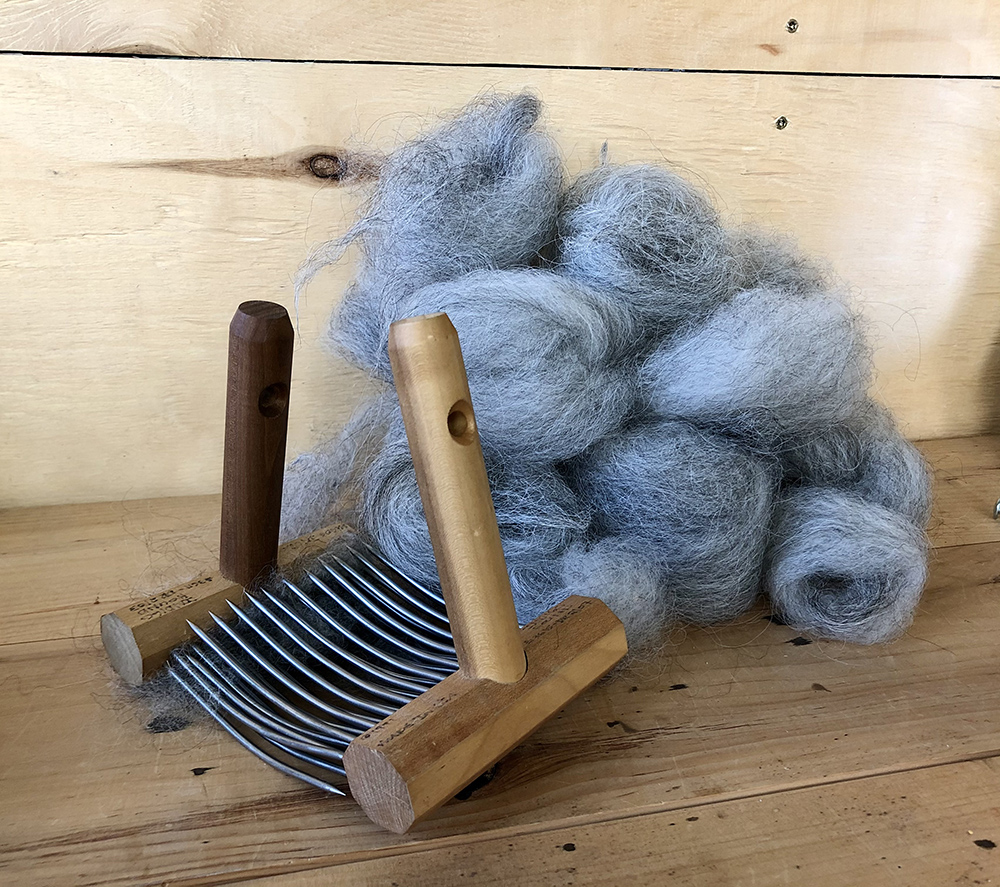
In her latest blogpost, resident Artisan Christine Novotny discusses the processing of wool from raw fleece and how it informs her weaving practice.
As of February 3, I have officially been in the Artisan Development Program 1 year. I’ve spent a lot of time reflecting on my accomplishments of the past year, and identifying what still needs my attention during this next year. I am feeling both a freedom toward embracing experimentation while also feeling the scarcity of time propel me! These two feelings culminated into a graceful permission to let the loom rest a bit (just a bit!) and do more learning in different areas. My focus this January has been doing a lot of natural dye experiments and beginning to work more with raw fiber.
Many of you may remember that I came to weaving through painting, a new pathway to create with color and texture with a tactile function. I had never done any fiber-related work before, and truly felt I was stepping into a new world with so much new vocabulary and processes. Yarn weights, yarn styles, fiber types, wool breeds - I learned as much as I could to guide my weaving and knitting, but not much beyond. While working a full time job and weaving as another full time job, it was difficult to dedicate time to the more foundational knowledge of how fiber transforms from sheep or plant to yarn. When I applied to the Artisan Development Program, I knew I wanted to backtrack a bit and dive more deeply into a material study. The summer of 2020 has been focused on growing, retting, and drying flax for linen. This winter has been focused on wool.
My materials mentor Andrea Myklebust sent me two raw fleeces shorn from her flock over the summer - a shetland named Bruna, and an icelandic named Othello. Over phone, email, and zoom, Andrea has been guiding me through wool processing step by step. I washed the fleeces in several batches in our shop sink at the studio, and reveled in the difference between the two! They turned from brown to a beautiful cool gray. Raw wool is very dirty!
Icelandic sheep Othello’s fleece, unwashed in the foreground, washed in the background
Then Andrea and I got together on zoom to do some wool combing and carding together. These processes arrange the fibers parallel to one another to prepare them for spinning. I have been focusing on wool combing Othello, a beautiful icelandic sheep with dual coated fleece. The outer coat is called tog, and has a texture like mohair. It has a long staple length which makes it quite strong, perhaps suitable to use as a warp yarn that is under tension on the loom. The fine undercoat is called pel (pronounced thel). The thel is a short and soft fiber, which would make lovely soft knitting yarn, or weft. When you use icelandic wool, you can card both coats together and spin it, or separate the tog from the thel with wool combs, and then use them separately to achieve different types of yarn.
Andrea sent along a pair of viking/peasant wool combs and a diz, two essential tools in the process of combing. Fiber is placed on one wool comb, shorn side in. I brace the fiber-filled comb against my knee, and it remains mostly stationary. The other comb combs the fibers at a perpendicular angle, until most of the fiber transfers to my moving comb. Then I switch and repeat the process. My moving comb becomes my stationary comb, and vice versa.
Combing the fibers
I do this a few times until the long fibers are well aligned.
A full comb of aligned fiber
I then use a diz to separate the long fiber. I am using a large button as my diz, but one could use almost any disk with a hole in it. I pull the tog through the hole in the diz into a long length, called a sliver.
Pulling the tog through the diz to create a sliver (doesn’t that sentence sound like nonsense?)
Once all the long tog fibers have been extracted from the comb, I gently wrap up the slivers around my hand and bundle them for storage until I’m ready to spin. The thel (short fibers) remain on the comb. Those could be combed again for spinning a soft yarn, or composted.
Thel (short fibers) on the left, Tog (long fibers) on the right
I have slowly been working away at the fleece and building up my slivers bit by bit. Andrea told me that it took 6 wool carders to keep one spinner busy, and 6 spinners to keep one weaver busy. We’re not sure if that is truly based in fact, but in my experience so far, it seems accurate!
Bundled slivers waiting to be spun
While I may not plan to process all my own fibers for my handwoven textiles in the future, becoming more intimate with the plants and animals that give us fiber is an incredibly important area of study for me. It builds reverence for these materials, roots me in textile history, and helps me better understand various yarn structures to create handwoven goods with different tactile qualities. I am grateful for this time to build my foundational fiber skills.